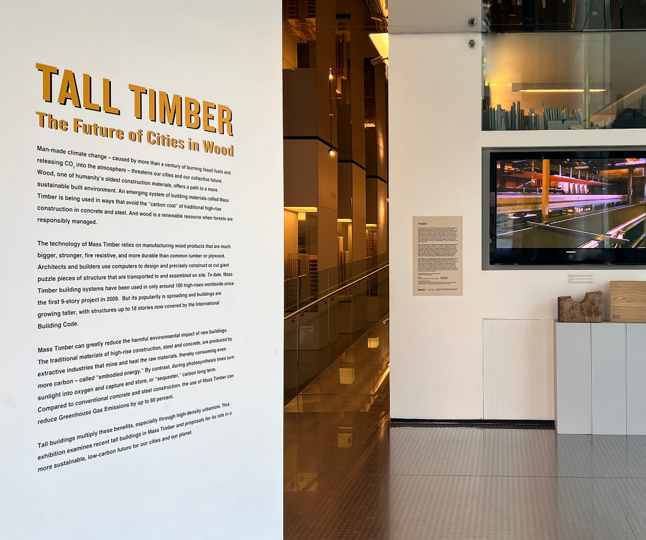
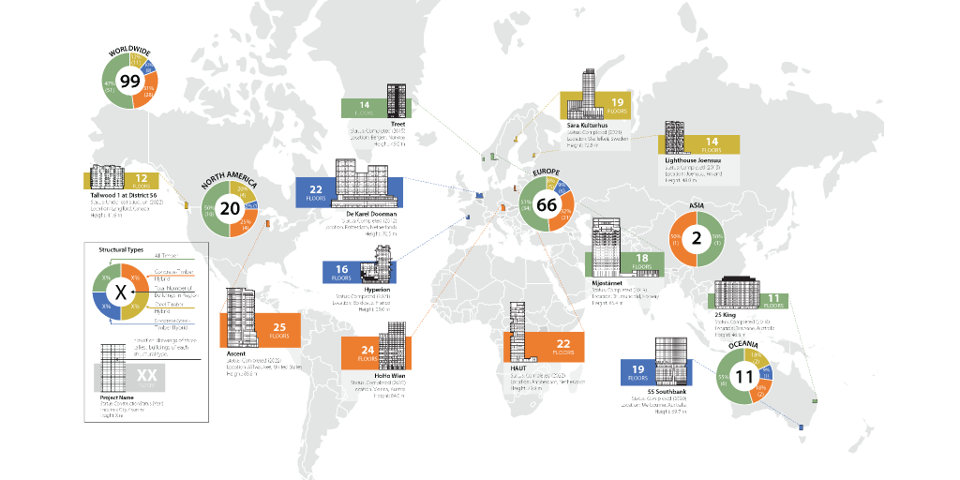
World map of tall Mass Timber buildings by the Council of Tall Buildings and Urban Habitat from Tall Timber: Mass Timber for High-Rise Buildings.

Man-made climate change – caused by more than a century of burning fossil fuels and releasing CO2 into the atmosphere – threatens our cities and our collective future. Wood, one of humanity’s oldest construction materials, offers a path to a more sustainable built environment. An emerging system of building materials called Mass Timber is being used in ways that avoid the “carbon cost” of traditional high-rise construction in concrete and steel. And wood is a renewable resource when forests are responsibly managed.
The technology of Mass Timber relies on manufacturing wood products that are much bigger, stronger, fire resistive, and more durable than common lumber or plywood. Architects and builders use computers to design and precisely construct or cut giant puzzle pieces of structure that are transported to and assembled on site. To date, Mass Timber building systems have been used in only around 100 high-rises worldwide since the first 9-story project in 2009. But its popularity is spreading and buildings are growing taller, with structures up to 18 stories now covered by the International Building Code.
Mass Timber can greatly reduce the harmful environmental impact of new buildings. The traditional materials of high-rise construction, steel and concrete, are produced by extractive industries that mine and heat the raw materials, thereby consuming even more carbon – called “embodied energy.” By contrast, during photosynthesis trees turn sunlight into oxygen and capture and store, or “sequester,” carbon long term. Compared to conventional concrete and steel construction, the use of Mass Timber can reduce Greenhouse Gas Emissions by up to 60 percent.
Tall buildings multiply these benefits, especially through high-density urbanism. This exhibition examines recent tall buildings in Mass Timber and proposals for its role in a more sustainable, low-carbon future for our cities and our planet.
The section of heavy timber was salvaged in the recent adaptive-reuse project of the landmarked Terminal Warehouse, designed by the architect COOKFOX for the developer L&L Holding Company.
Ancient Wood and Mass Timber
Wood is an ancient building material, but modern Mass Timber is an engineered product made in factories. These samples of heavy timber – a section of a column of the 1891 Terminal Warehouse in Manhattan hewn from a single giant pine – and a piece of modern glulam composed of ten layers of small boards laminated with adhesives for strength illustrate the essential nature of wood and advances in technology.
The video of a Kallesoe Machinery Cross Laminated Timber factory in Austria shows the massive scale and sophisticated mechanization of a process that requires few human workers. Courtesy of Kallesoe Machinery.
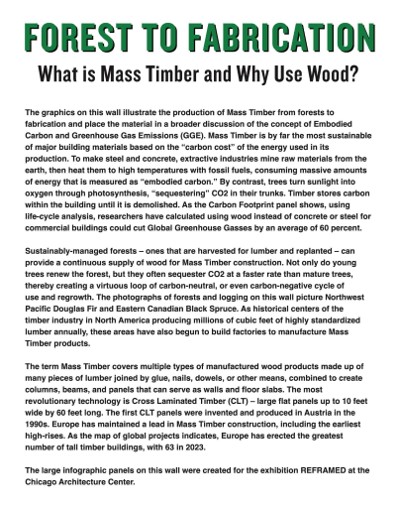
Forest to Fabrication: What is Mass Timber and Why Use Wood?
The graphics on this wall illustrate the production of Mass Timber from forests to fabrication and place the material in a broader discussion of the concept of Embodied Carbon and Greenhouse Gas Emissions (GGE). Mass Timber is by far the most sustainable of major building materials based on the “carbon cost” of the energy used in its production. To make steel and concrete, extractive industries mine raw materials from the earth, then heat them to high temperatures with fossil fuels, consuming massive amounts of energy that is measured as “embodied carbon.” By contrast, trees turn sunlight into oxygen through photosynthesis, “sequestering” CO2 in their trunks. Timber stores carbon within the building until it is demolished. As the Carbon Footprint panel shows, using life-cycle analysis, researchers have calculated using wood instead of concrete or steel for commercial buildings could cut Global Greenhouse Gasses by an average of 60 percent.
Sustainably-managed forests – ones that are harvested for lumber and replanted – can provide a continuous supply of wood for Mass Timber construction. Not only do young trees renew the forest, but they often sequester CO2 at a faster rate than mature trees, thereby creating a virtuous loop of carbon-neutral, or even carbon-negative cycle of use and regrowth. The photographs of forests and logging on this wall picture Northwest Pacific Douglas Fir and Eastern Canadian Black Spruce. As historical centers of the timber industry in North America producing millions of cubic feet of highly standardized lumber annually, these areas have also begun to build factories to manufacture Mass Timber products.
The large info-graphic panels on this wall were created for the exhibition REFRAMED at the Chicago Architecture Center.
Click on the slideshow for large legible panels.
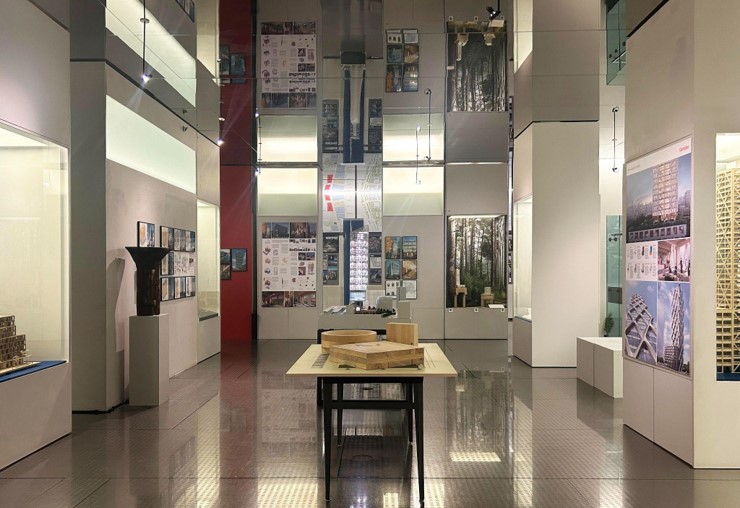
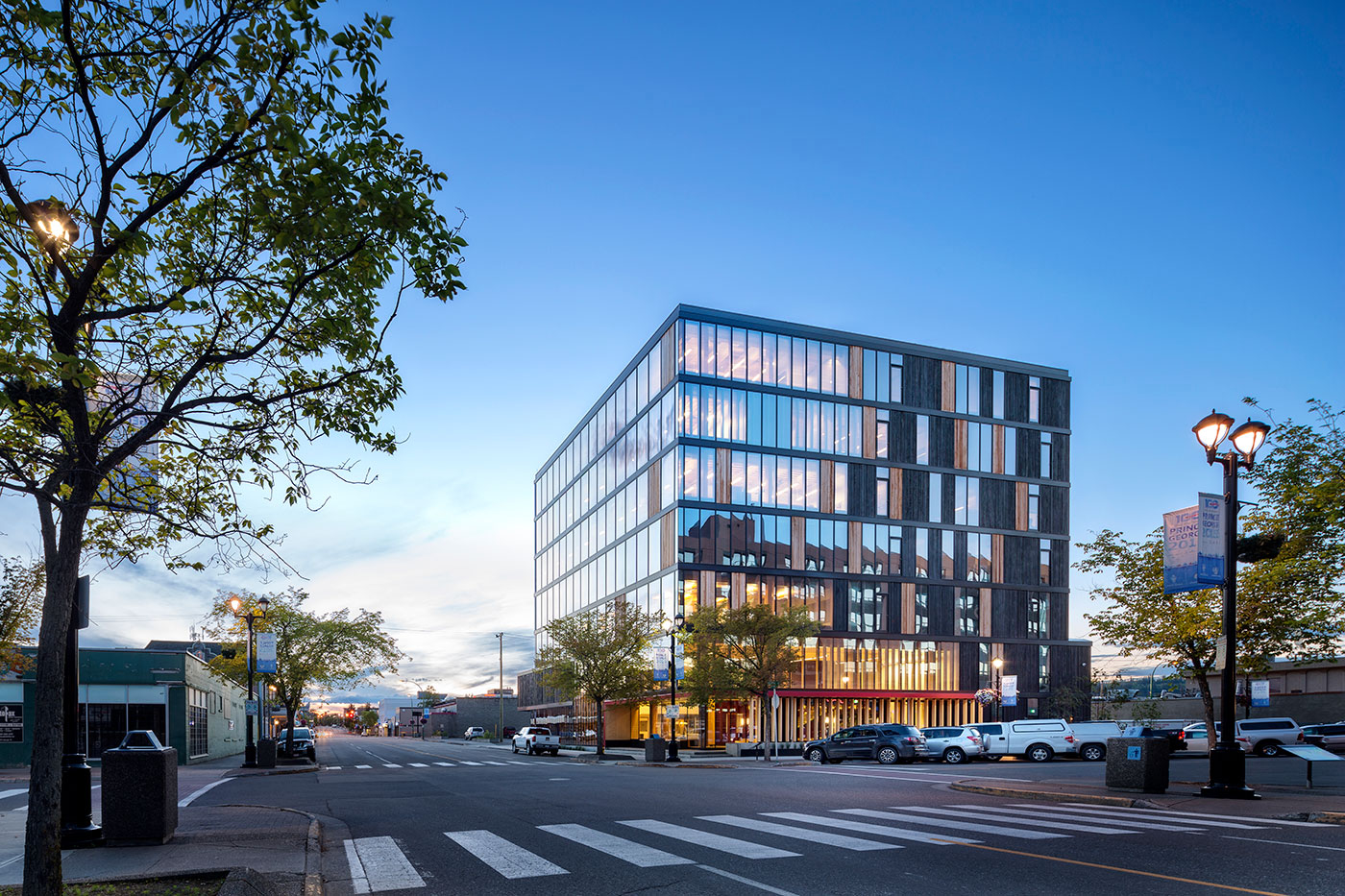
The Wood Innovation and Design Centre, in Prince George, Canada, was a government-sponsored project that, upon its completion in 2014, was the tallest modern all-timber structure in the world. Photo courtesy of Michael Green Architecture.
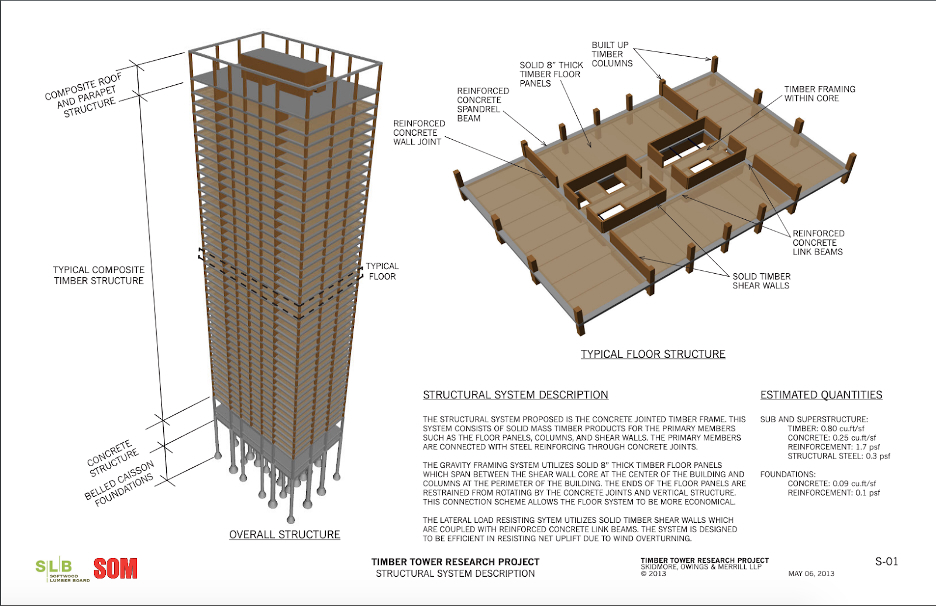
In 2013, architects and engineers at SOM applied their expertise in high-rise design to Mass Timber structures. They published their analysis of a 42-story composite timber and concrete structure as the Timber Tower Research Project Report. Drawing, p. 75.
The video shows excerpts of the construction of Albina Yard, a 4-story office building in Portland Oregon, designed by LEVER Architecture and completed in 2016. The prefabricated timber components arrived by truck, with the first 4,000 sf layer of CLT installed in less than four hours. Video courtesy of LEVER Architecture.
OVERVIEW: Themes and Featured Buildings
The Short History and Promising Future for Tall Mass Timber Buildings
Mass Timber has a short history – little more than a decade. The revolutionary technology of Cross Laminated Timber began production in the North American market around 2010, some two decades after European factories started to manufacture the large, strong structural panels. Early adoption came principally from areas with deep timber roots – largely in western British Columbia and the Pacific Northwest – and was embraced by a handful of architects, engineers, and academics who were committed to the structural, sustainable, and aesthetic nature of wood products, but who built only at small scale. Even in Europe, CLT was not used for high-rises until 2007. The first Mass Timber buildings in North America of 8 stories were completed in 2014.
Highlighting the early designs for multi-story Mass Timber, the exhibition charts the growing commitment to the virtues of wood in the design and building communities, but slow progress of completed buildings. From around 2012, U.S. and Canadian government agencies funded innovations through competitions and grants for research. Universities were centers for discussion, especially around issues of embodied carbon and sustainability. Regionalism played an important role, especially in the Pacific Northwest, and annual Mass Timber conferences created a close community of advocates, designers, and material producers.
Inspired by the new technology around Mass Timber, as early as 2014, some architects and engineers in larger firms pursued studies for tall towers of 30 to 80 stories, bringing their experience with high-rise planning and construction to the analysis, along with their concern for carbon costs and sustainability. Such visions were, of course, outside real-world regulation. Mass Timber buildings taller than 9 stories were constrained by conservative codes, although an 18-story dormitory in Vancouver, Brock Commons, was completed in 2017 as a demonstration project. In 2022, Ascent, a 25-story apartment and mixed-use tower with 18 stories of Mass Timber erected over a 7-story concrete base, opened in Milwaukee, becoming the world’s tallest Mass Timber building. The International Building Code (IBC) officially approved a standard code for Mass Timber in the U.S. for buildings of 18 stories in 2021, ushering in a new realm of opportunity for the industry. The promise of Mass Timber, however, lies in increasing both demand and supply.
The advantages of CLT for high-rise construction are many. The large factory-made panels of up to 10 feet wide by 60 feet long are extremely strong and very light compared to steel or concrete. The panels are precisely cut in the same factory by large CNC machines into the bespoke elements of the 3D plans of the designers. They arrive at the site as a kit of parts and are erected with cranes in a construction process that is fast and clean, reducing the number of workers on site and thus construction costs, as the videos in the exhibition attest. On the interiors, the exposed wood has a distinctive and pleasing aesthetic and biophilic properties for inhabitants. On a global scale of climate, the widespread adoption of Mass Timber from responsibly managed forests would sequester carbon and help move the building industry from its position as a major contributor to Greenhouse Gas Emissions toward a more carbon-neutral future.
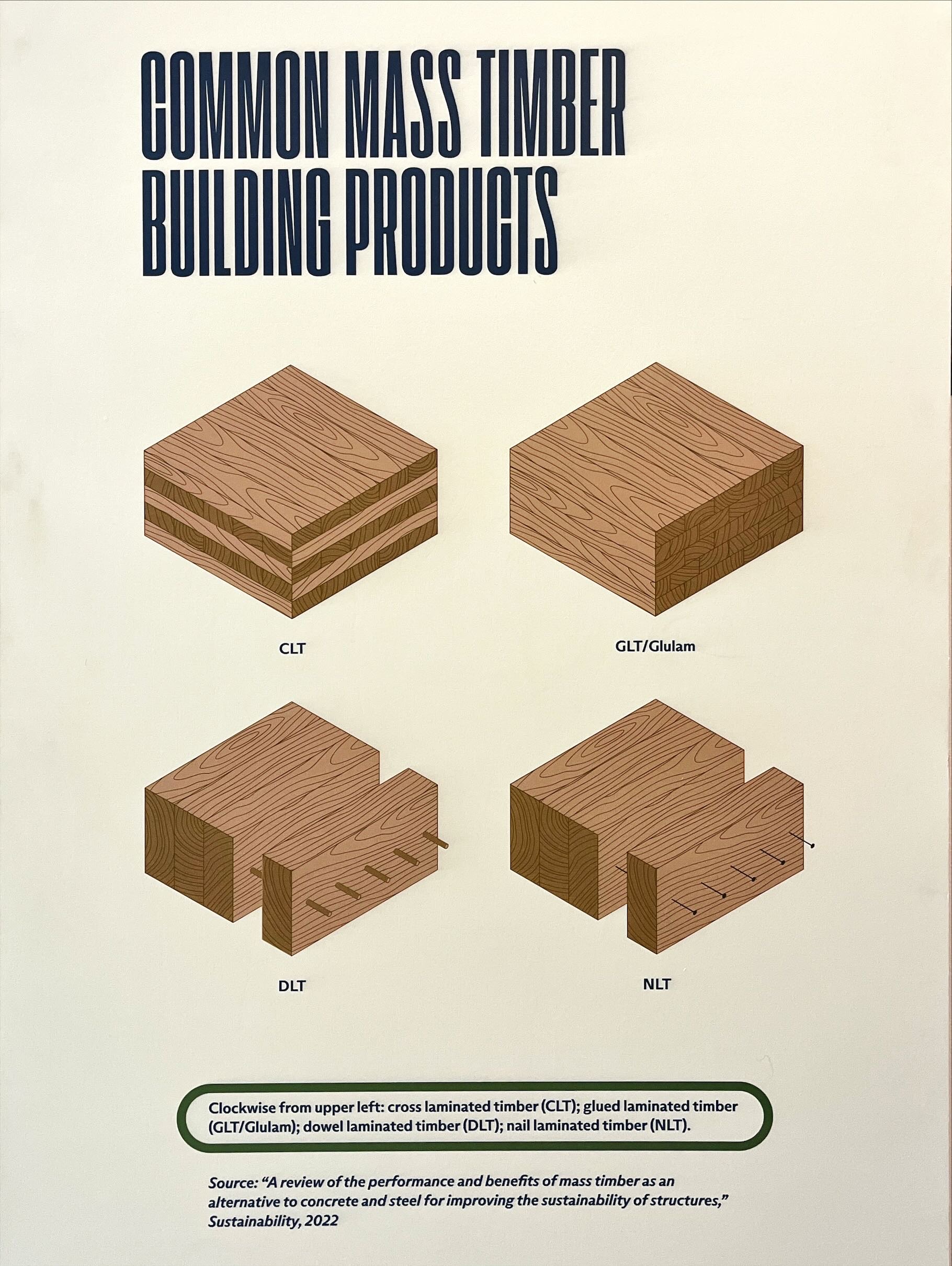
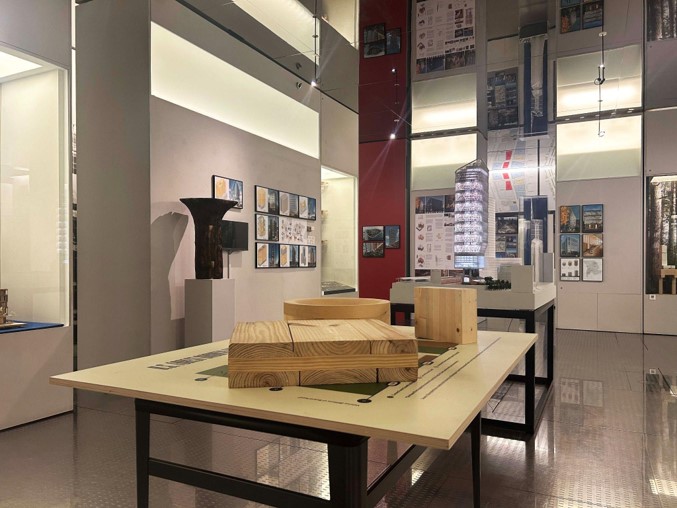
MASS TIMBER PRODUCTS
The term Mass Timber covers multiple types of engineered wood products – large structural members that are manufactured in factories from small pieces of standard milled lumber. Illustrated on the left are different methods of joining individual boards into larger and stronger elements, either by wooden dowels or with nails, or with adhesives, as in the case of glulam and Cross Laminated Timber (CLT).
CLT is a new technology that far surpasses the age-old technique of glulam, in which all the wood grain runs in the same direction and which is still used for columns and beams. Large, strong panels that measure up to 10 feet wide by 60 feet long and can serve as structural walls, floor slabs, and roofs are produced by gluing together many small boards into a layer, or lamella. Each lamella alternates direction as it is pressed into the base panel so the grain crosses at 90 degree angles, which greatly increases the strength of the material in tension. Generally, CLT is produced in layers of 3-5-7-9 lamellas. Compared to steel or concrete structures, based on weight, CLT is immensely strong: it is also carbon neutral or carbon negative.
The technology of Cross Laminated Timber was first researched and developed in Austria in the 1990s and Europe has the largest and most sophisticated factory production of the material. The adjacent photographs show various stages in the factory production of CLT in a Nordic Structures facility in northern Quebec that uses small-diameter Black Spruce harvested from forests they own and manage.
The Mass Timber graphic was created for REFRAMED at the Chicago Architecture Center.
Michelle Roelofs, Associate Principal and Structural Engineer at Arup, and Tanya Luthi, Director of Engineering at Timberlab, presented a primer on the history and types of Mass Timber and explained its virtues and challenges in a lecture for the Museum. Watch "MASS TIMBER 101" here.
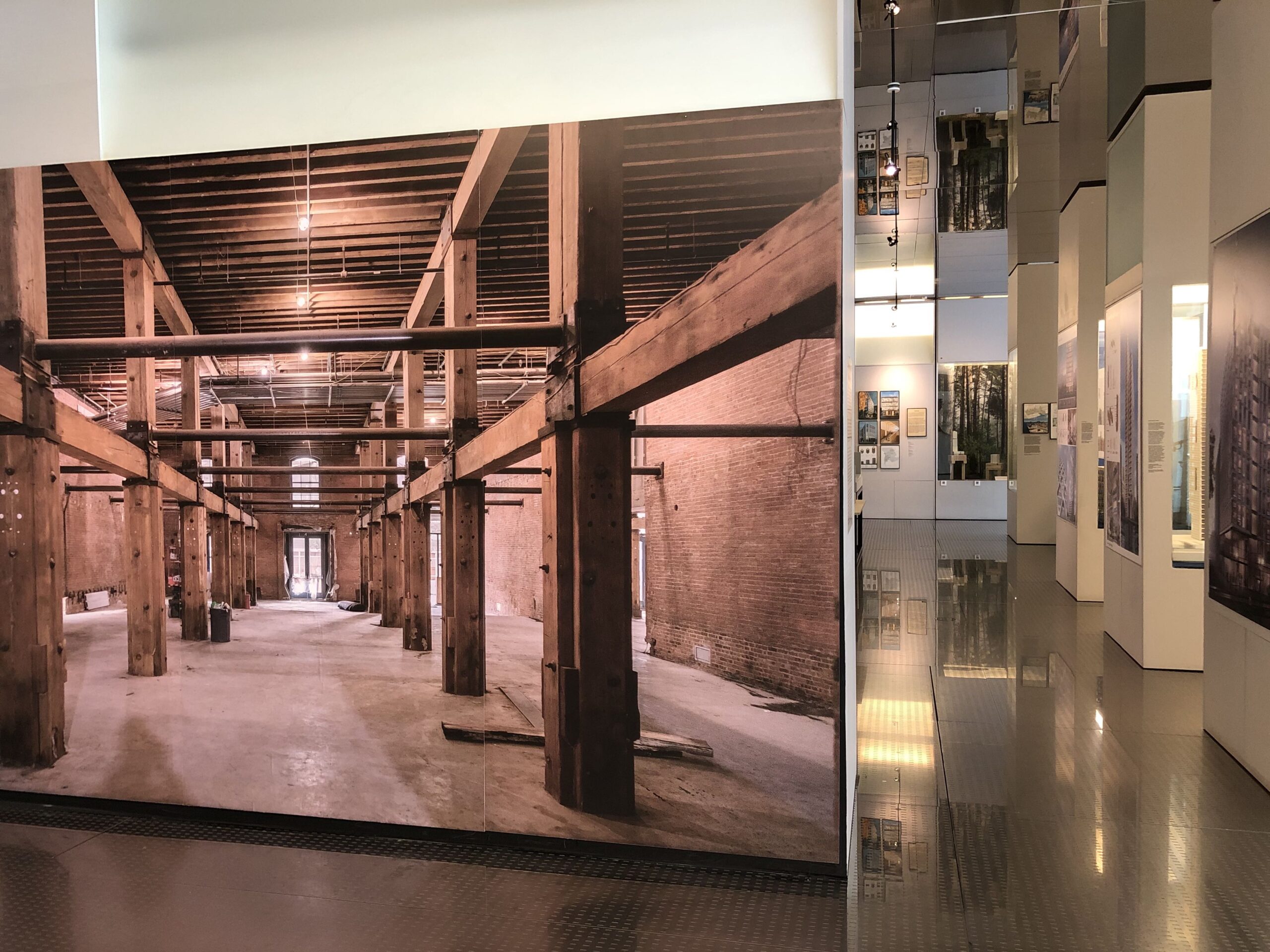
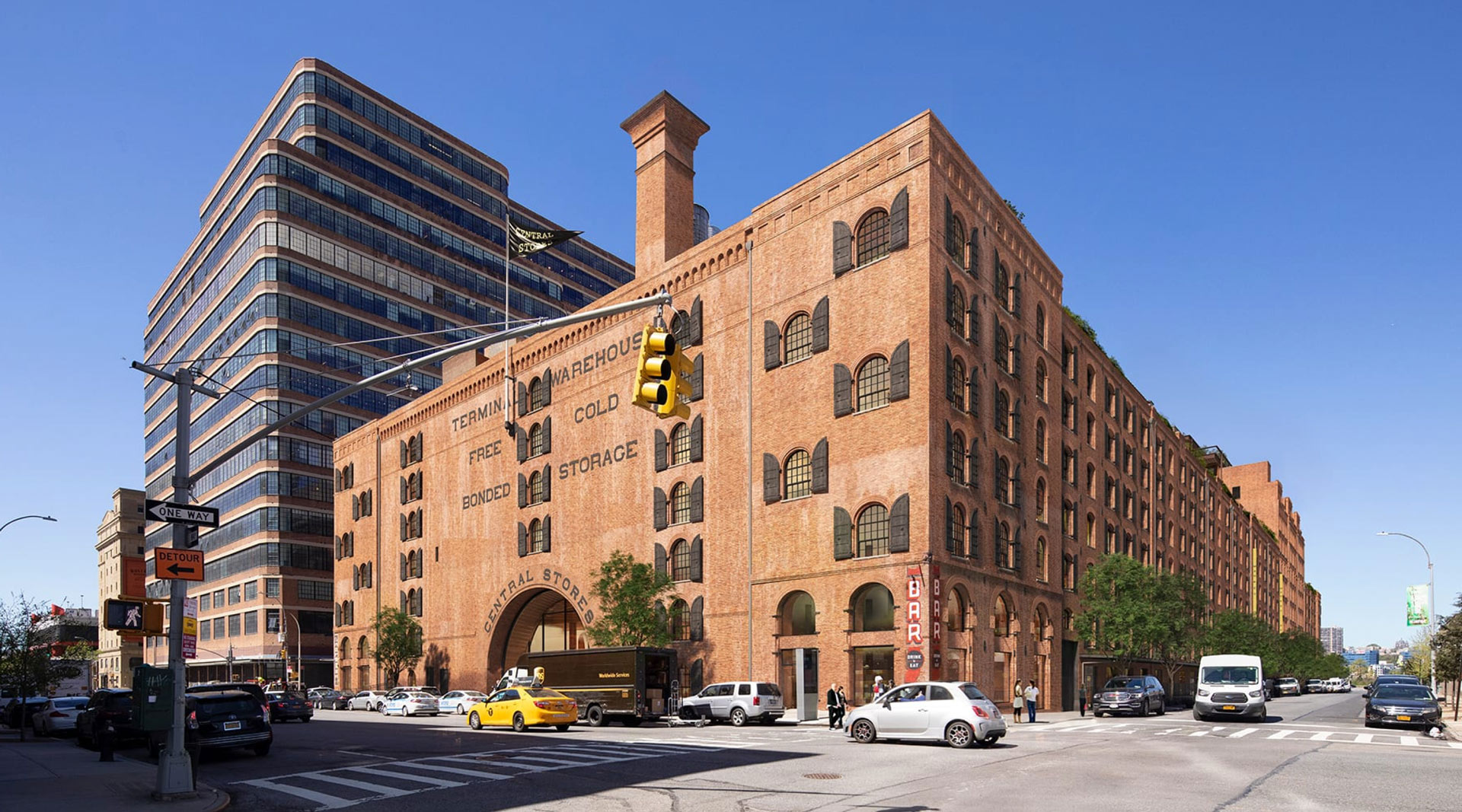
Courtesy of L&L Holding Company.
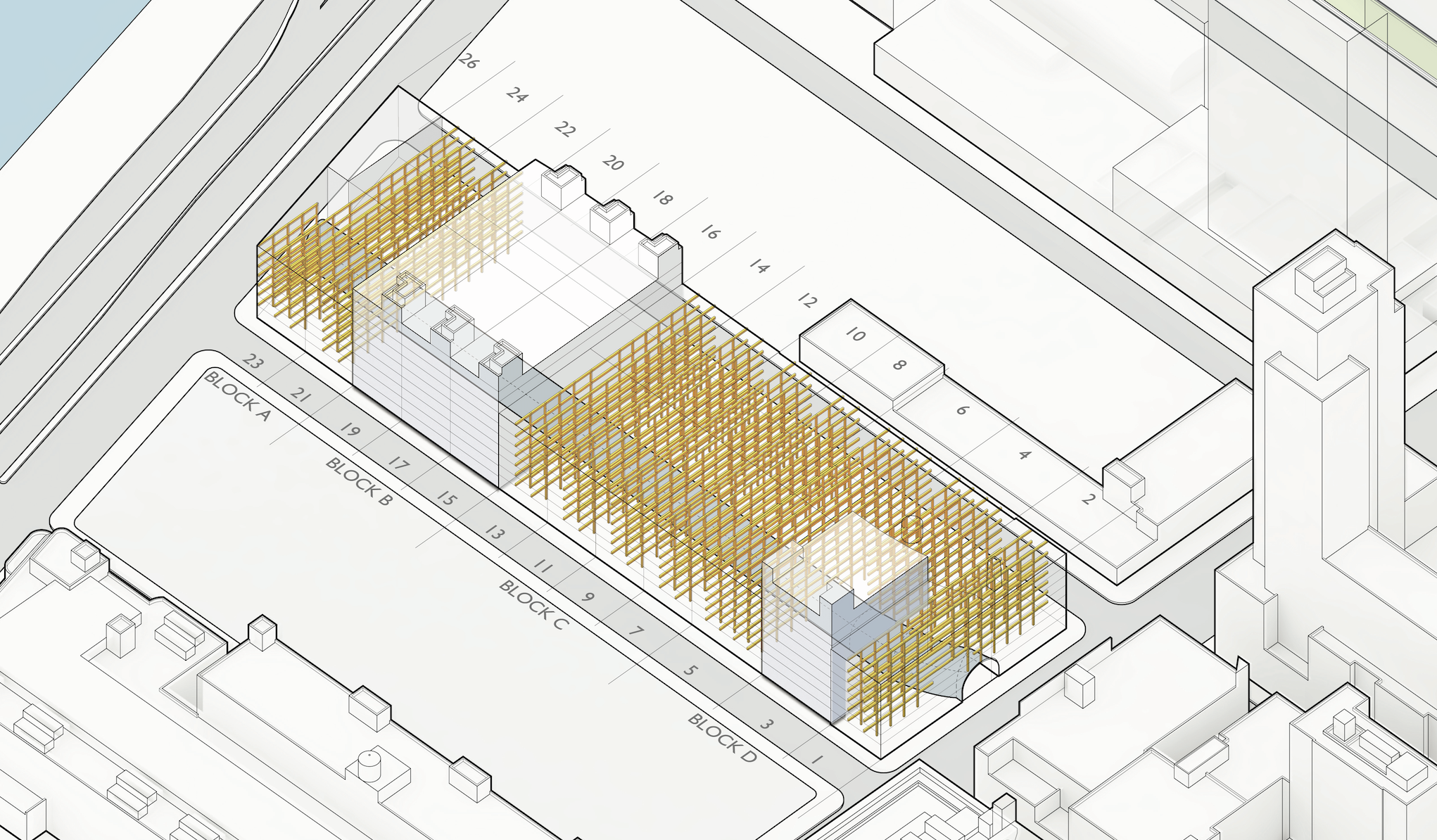
Courtesy of COOKFOX Architects.
The Timber Tradition in American Building
Timber enabled the U.S. to grow and industrialize. Railroad ties and trestle bridges allowed trains to transport logs and lumber to central cities and heavy timber served as the structure for columns and beams through the late 19th century, as can be seen in the interior of New York’s Terminal Warehouse in the photo mural on the right. At the same time, standardized two-by-fours could be shipped by train across the country to turn the balloon frame or “stick-built” house into a characteristic American architecture, as it remains today.
Terminal Warehouse
Erected in 1891, the Terminal Warehouse Stores on Manhattan’s Far West Side between 27th and 28th streets had a masonry exterior of brick, but relied on an interior structure of heavy timber. Railroad cars could roll directly into the building from tracks along the waterfront into the central “tunnel” to off-load goods among the massive timber columns that carried the gravity loads of the building’s six stories. These columns were hewn trunks of ancient trees, logged and transported by railroad from a forest in Georgia that a Columbia University dendrochronologist has dated to the early 1500s. A section of one of these columns can be seen at the entrance of the exhibition. The photomural to the right shows the restored interior that is part of the preservation and transformation of the buildings by the developer L&L Holding Company into a mixed commercial and office complex. COOKFOX Architects, a practice deeply committed to biophilic design principles, led the design team for the adaptive reuse project.
Original Architect: George Mallory
Developers: L&L Holding Company, Columbia Property Trust, and Cannon Hill Capital Partners
Preservation Architect: COOKFOX Architects
Structural Engineer: DeSimone Engineering

FRAMEWORK
This project by LEVER Architecture – called Framework to reference a "Forest to Frame” concept of domestically sourced CLT – was the co-winner of a 2015 national competition for the U.S. Tall Wood Building Prize, directed at stimulating innovation in high-rise applications in Mass Timber construction. The role of government was important: the competition was sponsored and funded through a public-private partnership headed by the U.S. Department of Agriculture (USDA), the Softwood Lumber Board (SLB), and the Binational Softwood Lumber Council (BSLC). The model of the other winner, a New York City project, 475 W. 18th Street, is on display in the vitrine opposite.
Based in Portland, Oregon, LEVER, led by architect Thomas Robinson, designed the 12-story mixed-use building to combine retail and public exhibition space on the ground floor with five levels of offices and 60 units of affordable housing. Research to continue the Framework proposal was supported by a $1.5 million grant that offset costs of testing and peer review, which included full-scale fire testing and seismic testing of a new timber “rocking wall” technology that self-centers in earthquakes. Although the design was fully permitted in Oregon, in 2018 the developer decided not to move forward with the project. Nevertheless, Framework became the model of the Type IV-B high-rise Timber code.
Architect: LEVER Architecture
Engineers: KPFF & Arup
Developer: project^
Model courtesy of LEVER Architecture
To learn more about Framework and 475 W. 18th Street, hear from the architects themselves as part of the Museum's TALL TIMBER lecture series: Bicoastal Beginnings and Where are We Now?
475 West 18th Street, New York City
The co-winner of a 2015 national competition for the U.S. Tall Wood Building Prize, along with the Portland, Oregon project Framework, was the design for 475 W 18th St., a 10-story apartment building in West Chelsea near the High Line. The photographs show the award ceremony held on one of the High Line’s gathering spaces. At the podium is the project’s development manager Jeff Spiritos of Spiritos Properties, flanked by government officials and sponsors of the competition, including U.S. Secretary of Agriculture Tom Vilsack. Each of the competition’s winners were promised $1.5 million in funding to support the research and development necessary to advance the project.
This model by SHoP Architects was developed after the prize was awarded to advance their design concept. It details two stories of the Mass Timber structure, with its glulam columns and beams, and CLT floors that were topped with a two-inch layer of concrete and acoustic underlayment, covered by an engineered hardwood floor finish. Because the NYC building code prevented timber construction taller than 6 stories, the design team of SHoP and Arup, the structural, fire, and acoustic engineer, were obliged to do full scale performance-based structural and fire testing to receive a variance. The sustainability consultant Atelier Ten targeted reducing overall energy consumption by at least 50 percent of current energy codes. Despite developing a Construction Code Determination (CCD1) and full-scale testing program developed in collaboration with the NYCDOB and FDNY, the permitting process proved challenging politically and in the end union objections stymied the project.
Architect: SHoP Architects
Development Manager: Spiritos Properties
Engineers: Arup and Icor Consulting Engineers
Environmental Consultants: Atelier Ten
ACADEMIC AND PROFESSIONAL RESEARCH
Universities and Schools of Architecture were important centers for discussion around the issues of the climate crisis, life-cycle analysis, embodied carbon, and the responsibility of the design community to face their role in these problems. The drawings displayed here represent studies on these issues. The earliest are the 2010 transect analyses of building materials and their carbon costs and the proposal for creating Mass Timber housing through a continuous loop of harvesting timber and replanting forests by Alan Organschi, an architect and professor at Yale who headed their research project Timber City. The other drawings are the recent studies of Lindsey Wikstrom which apply a similar analysis of the carbon consumption of a typical suburban-versus-urban lifestyle and the number of trees required to store that carbon. Her panoramic sketch of the “Mass Timber Material Story” pictures steps from production through construction. These drawings are illustrations in Wikstrom’s 2023 book Designing the Forest and Other Mass Timber Futures.
Research within architectural and engineering firms was also important. SOM’s 2013 Timber Tower Research Project is represented here in two pages of a 105-page report. In it the firm’s engineers explored how their expertise in high-rise design could be translated into Mass Timber structures. Their benchmark was based on the Dewitt-Chestnut Apartments, a 42-story building in Chicago constructed in 1966. Their solution was the "Concrete Jointed Timber Frame," which relied on mass timber for the main structural elements with supplementary reinforced concrete at the connecting joints.
Watch Lindsey Wikstrom's presentation on managed forests and Mass Timber in a talk on her book Designing the Forest here.
RIVER BEECH TOWER
As early as 2013, some architects and engineers in larger firms pursued studies for Mass Timber towers of 30 to 80 stories, bringing their experience with high-rise planning and construction to the analysis, along with their concern for carbon costs and sustainability.
In 2014, architects in the Chicago office of Perkins + Will teamed up with researchers at Cambridge University in England and structural engineers at Thornton Tomasetti to propose an 80-story apartment tower in Mass Timber. The site was real – a section of the Chicago River that was the focus of the city’s master plan for new development– but at 748 ft./ 228 meters, the design was highly theoretical, since the International Building Code was, at the time, limited to 85 ft stories.
Named River Beech Tower, the structure took the form of two narrow slabs joined by an atrium, laced together by intersecting diagonal beams. The exterior walls are a load-bearing diagrid or honeycomb-like structure that carry most of the weight of the building. The tower contained 300 duplex units arranged in twin single-loaded bars around a central atrium. The plan was chosen to study the opportunities for modularity and prefabrication, as well as to incorporate the basic building blocks for through-unit cross ventilation and opportunities for vertically accessible community and amenity spaces.
Architect: Perkins+Will
Timber Research: University of Cambridge
Structural Engineer: Thornton Tomasetti
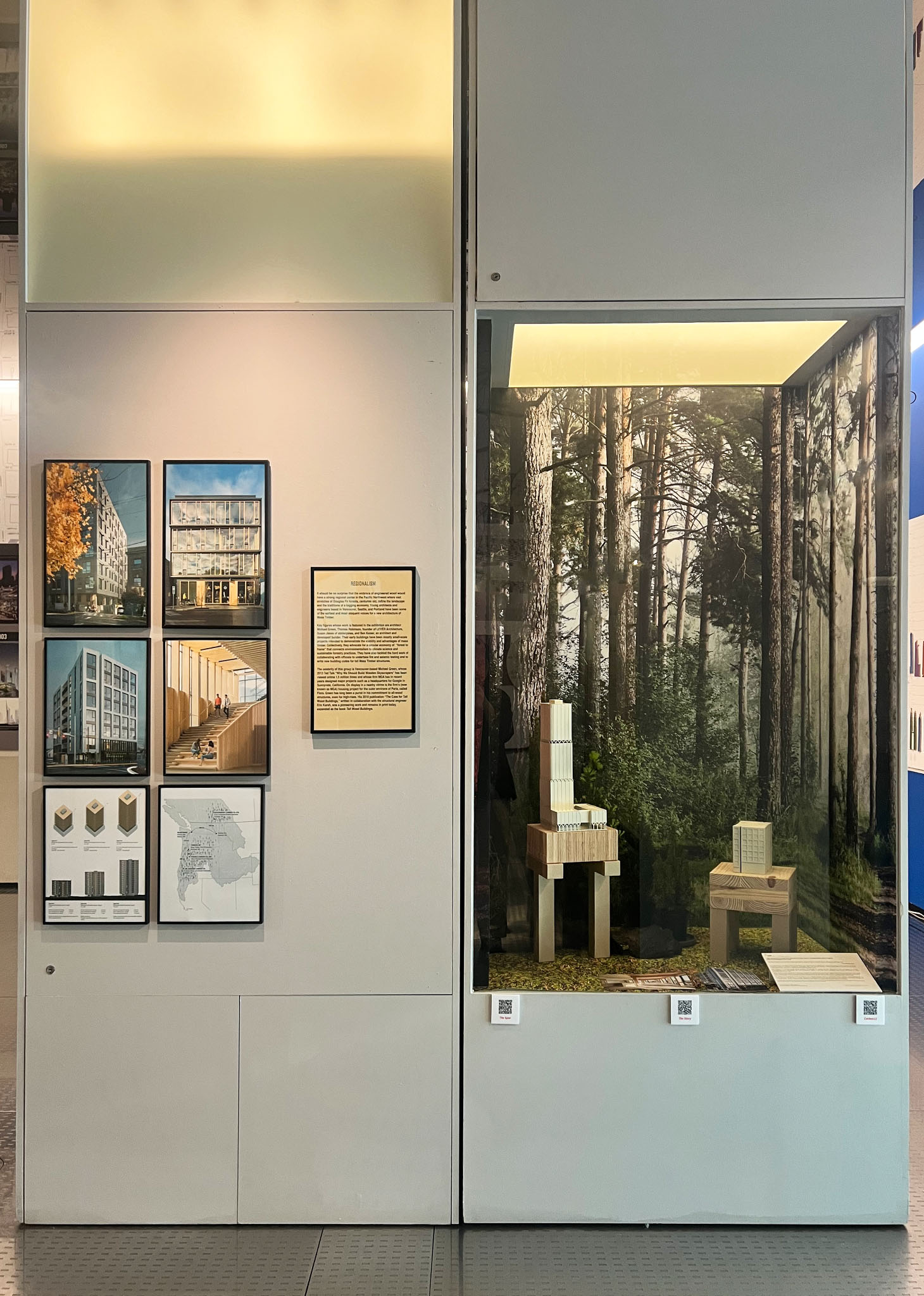
REGIONALISM
It should be no surprise that the embrace of engineered wood would have a strong regional center in the Pacific Northwest where vast stretches of Douglas Fir forests, centuries old, define the landscape and the tradition of a logging economy. Architects and engineers based in Vancouver, Seattle, and Portland have been some of the earliest and most eloquent voices for a new architecture of Mass Timber.
Key figures, whose work is featured in the exhibition, are architect Michael Green, Thomas Robinson who heads the firm LEVER Architects, Susan Jones of atelierjones, and Ben Kaiser, an architect and developer/ builder. Their early buildings have been mostly small-scale projects intended to demonstrate the viability and advantages of mass timber. Collectively, they advocate for a circular economy of “forest to frame” that connects environmentalism to climate science and sustainable forestry practices. They have also tackled the hard work of collaborating with officials to undertake fire and seismic testing and to write new building codes for Mass Timber structures.
The early celebrity of this group is Vancouver-based Michael Green, whose 2013 Ted Talk “Why We Should Build Wooden Skyscrapers“ has been viewed online 1.5 million times and whose firm MGA has in recent years designed major projects such as a headquarters for Google in Sunnyvale, California. On display in a nearby vitrine is the firm’s (now known as MGA) housing project for the outer environs of Paris, called Flora. Green has long been a purist in his commitment to all-wood structures, even for high-rises. His 2010 publication “The Case for Tall Wood Buildings,” written in collaboration with the structural engineer Eric Karsh, was a pioneering work and remains in print today, expanded in the book Tall Wood Buildings.
Heartwood, Seattle, 2023
atelierjones; DCI Engineers, Bergelectric Corp., HV Engineering
Albina Yard, Portland, 2016
LEVER Architecture; KPFF Consulting Engineers
Carbon12, Portland, Oregon, 2018
Kaiser+Path; Munzing Structural Engineering, LLC
Wood Innovation & Design Centre, Prince George, CA, 2014
Michael Green Architecture; MMM Group
International Building Code Type IV Buildings
atelierjones
Timber Sourcing Map
atelierjones
Discover more about Heartwood and mass timber building codes from Susan Jones in the video of her lecture at the Museum: Mass Timber by Code and at Scale.
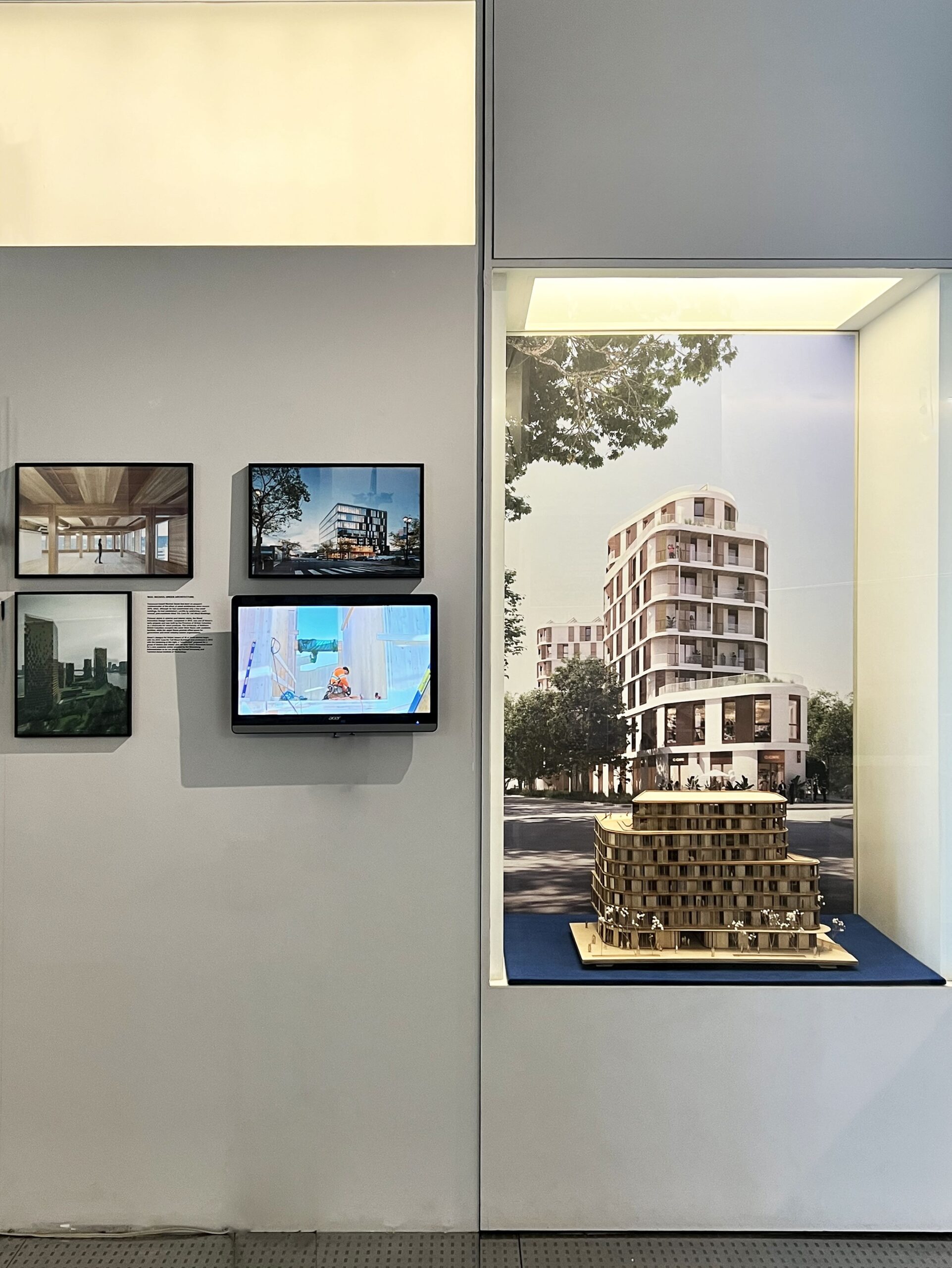
MGA: MICHAEL GREEN ARCHITECTURE
Vancouver-based Michael Green has been an eloquent communicator of the ethos of wood architecture since around 2010, when, although he had constructed only a few small buildings, he had established a profile by publishing a part-manual, part-manifesto titled The Case for Tall Wood Buildings.
Pictured above in exterior and interior views, the Wood Innovation and Design Centre, completed in 2014, was one of Green's early projects and was built by the Province of British Columbia as a showcase for wood products. The University of Northern British Columbia occupies the lower three floors with academic facilities, while the upper floors provide office space for government and wood industry-related organizations.
Green's designs for timber towers of 30 or more stories begin with his 2010 The Case for Tall Wood Buildings and continued in 2012 with the rendering at the right, a “unsolicited” proposal for a group of towers and master plan for New York’s Roosevelt Island for a new academic center planned by the Bloomberg Administration to be run jointly by Cornell University and Technion-Israel Institute of Technology.
The detailed wood model in the adjacent case underscores the commitment to an all–wood approach to design advocated by Michael Green Architecture. The building is a 9-story mixed-use complex that offers 7 levels of market, intermediate, and social housing, as well as commercial spaces including retail, offices, and co-working. Named Flora, the project, which will open in spring 2024, is part of a new neighborhood in Nanterre, a suburb of Paris.
Green summarized the history and evolution of tall wood buildings at the Museum. Watch the video of his lecture, The Evolution of Mass Timber, here.
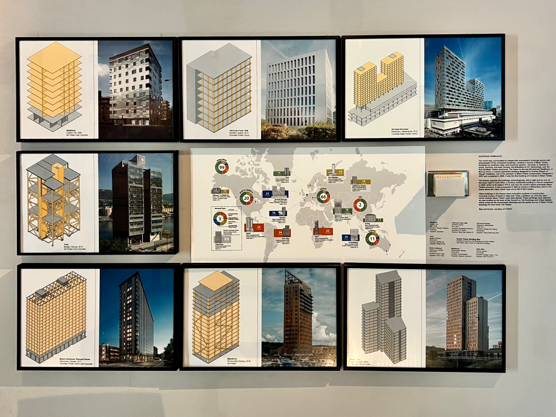
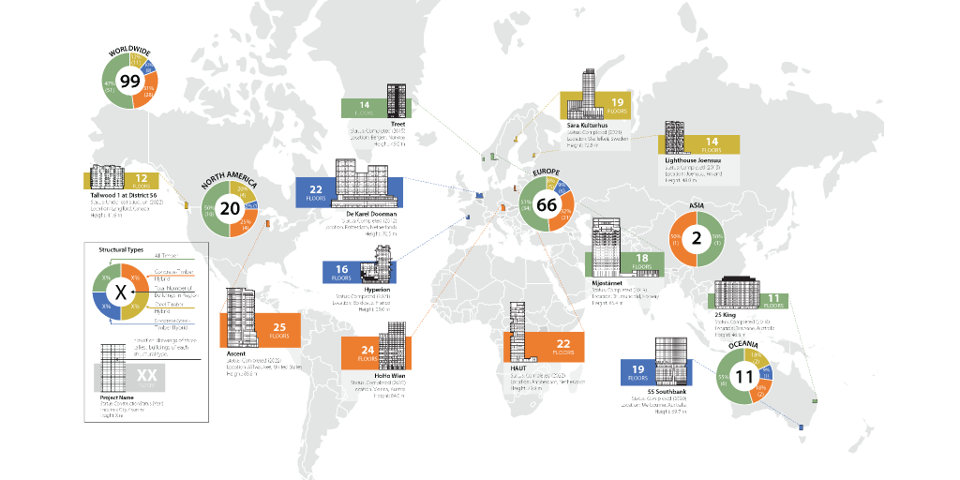
World map of tall Mass Timber buildings by the Council of Tall Buildings and Urban Habitat from Tall Timber: Mass Timber for High-Rise Buildings.
EUROPEAN DOMINANCE
The world map, surrounded by frames with axonometric drawings paired with photographs of the completed buildings, contains a survey of Mass Timber buildings by continent, date, and structural system – all wood, or hybrids of wood, concrete, and steel. Europe, the birthplace of CLT technology, saw the first tall Mass Timber structures. The frame on the top left pictures Stadthaus, or Murray Grove, a London apartment building designed by Andrew Waugh of Waugh Thistleton, one of the pioneers of Mass Timber construction. Designed in 2007 and completed in 2009, it was the first building of 9 stories in Mass Timber.
The frames organize the buildings chronologically, left to right and by row. At the lower right is HoHo Wien, a 23-story residential building in Vienna completed in 2020, which at 84 meters/ 276 ft. was then the world’s tallest principally Mass Timber structure. It was surpassed in 2022 by Ascent in Milwaukee, seen in the frame above the video, which tops out at 284 ft/ 86.6 meters.
Other buildings in the frames show innovative systems of construction, including trusses of wood or steel and, Treet, a platform on concrete upon which modular Mass Timber units were placed. These buildings were selected as case studies by the team of the Council on Tall Buildings and Urban Habitat, which prepared the axonometric drawings and the global survey of Mass Timber buildings for their book Tall Timber.
Map and Axonometric Drawings, courtesy of CTBUH
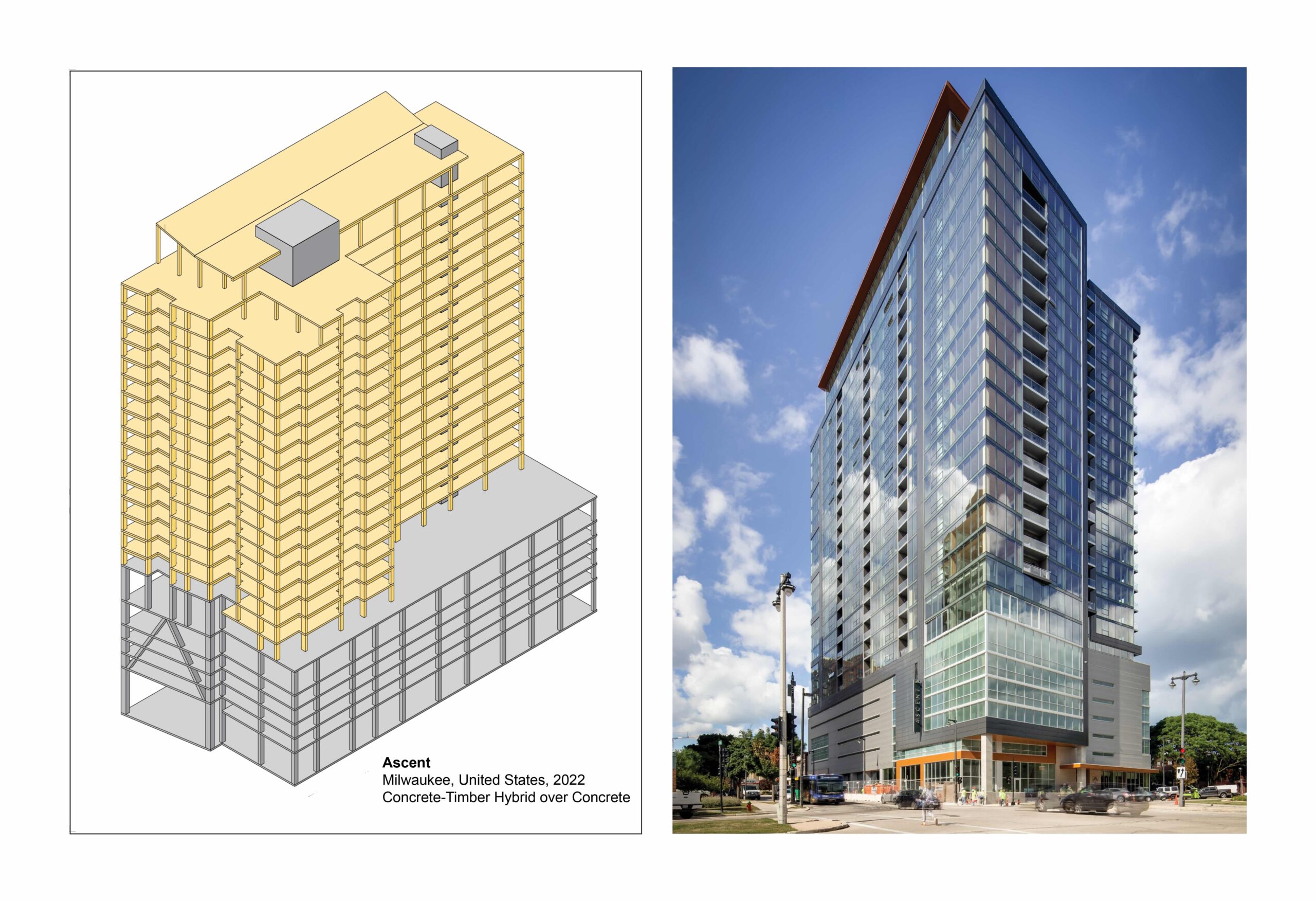
Ascent
Milwaukee, WI
2018-2022
Architects: Korb + Associates
Engineer: Thornton Tomasetti
ASCENT
Ascent, a 25-story apartment and mixed-use tower with 18 stories of Mass Timber erected over a 5-story concrete base, opened in Milwaukee, Wisconsin in 2022. It currently holds the titles for tallest Mass Timber building in the world by vertical height (284 ft./ 86.6 meters), as well as tallest timber-hybrid building. Completed before the International Building Code was revised upward from 12 to 18 stories, Milwaukee officials required Ascent’s developer, architect, and engineer to perform extensive testing, including the 3-hour burn test of the Glulam column shown on the adjacent video monitor and evidenced in the remnants of the charred column.
The architect Korb Associates and engineer Thornton Tomasetti worked together to design the structure by computer modeling. All the details of the Mass Timber structure were specified in the digital model, which was then given to the CLT manufacturer – in Europe – for production. The wood components were precisely cut and shipped to Milwaukee. Ultimately, though, the “kit of parts” of engineered wood was quickly assembled by a small team of construction workers at the rate of one floor a week, proving the economic and time advantages of Mass Timber, especially as compared to standard concrete frame construction.
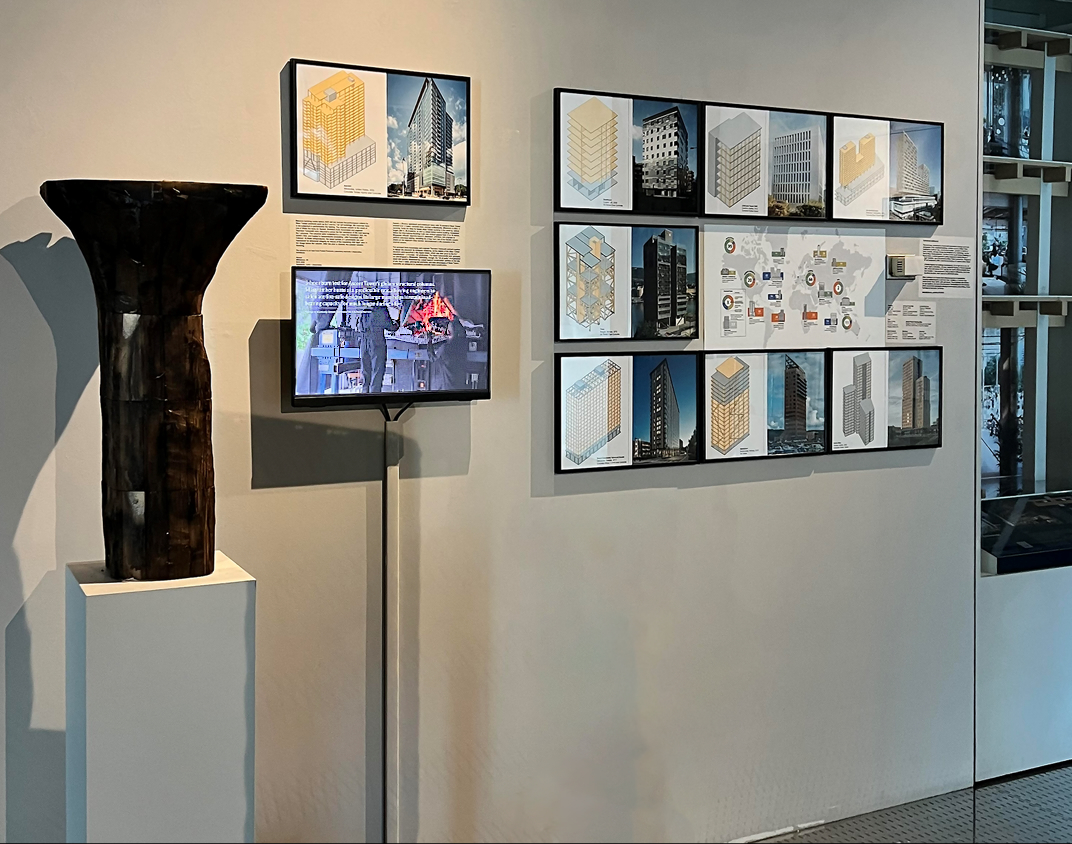
The column is on loan from Forest Products Laboratory via Korb + Associates Architects.
CHARRED COLUMN
Because building codes before 2021 did not include fire-performance criteria for Mass Timber products such as GLT and CLT for tall buildings, the materials have to be subjected to performative fire testing. The charred column is the result of one of these fire tests for Ascent. Architect Korb Associates and engineer Thornton Tomasetti were required to prove the fire resistance of the load bearing, GLT columns. The columns were subjected to a 3-hour fire resistance test, the world’s first, and heated to temperatures exceeding 1,800 Fahrenheit (982 Celsius). At these temperatures, the wood burned at a predictable rate and maintained its structural integrity by means of the insulating char layer seen in the image below the column. After the char is cleared, the column remains standing.
SCALING UP
The embrace of Mass Timber by corporations such as Alphabet and large real estate developers can help the process of scaling up the production of material by creating a consistent demand.
WATERFRONT TORONTO
The old industrial waterfront of Toronto is currently being redeveloped under a master plan overseen by the city as a residential and mixed-use community through the mechanism of a public-private partnership – much like Battery Park City was created. The planning process involved the strategy of awarding a large site to a single developer to take a comprehensive approach to both creating the infrastructure and designing and erecting all the buildings.
In 2017, Sidewalk Labs, a Google/Alphabet subsidiary, was selected to develop a 12-acre site called Quayside, on which they planned a $1.3 billion “smart city” they declared would be “the most innovative district in the entire world.” Many well-known architects were commissioned to design mixed-use and residential high-rise complexes, including Michael Green Architecture (MGA), Snøhetta, and Thomas Heatherwick, but the constant in their brief was utilizing Mass Timber. Sidewalk Labs also envisioned financing a new, local mass-timber industry that would manufacture the materials and prefabricate modules of the 12-story wooden high-rises. That large-scale effort and investment collapsed in May 2020 for a host of reasons.
PROTO-MODEL X
The Toronto office of the large international firm Gensler, stretched the “kit of parts” – a concept developed by MGA – to 35 stories, twice the height of any existing Mass Timber building. Their Proto-Model X (PMX) project was a pure-timber tower designed as a “digital proof-of-concept.” They developed the complete design of the architectural program and engineering and construction details in a 3-dimensional computer model that could be tested for its performance in earthquakes and high wind conditions, among other factors.
The structure used an external cross-brace frame made of CLT that, along with the CLT core, carried the gravity and lateral loads and allowed for an open floor plan. The lightness and flexibility of the wood at the 35-story height was stabilized by a tuned mass damper at the building’s top. The tower program mixed retail on the ground floor with office, live-work, and traditional residential units above.
Gensler continued to elaborate the concept of PMX after Sidewalk Labs dropped their plans for Quayside.
Architect: Gensler
Engineers: Aspect Structural Engineers
Developer: Sidewalk Labs
Model courtesy of Gensler
T3 BAYSIDE
The adjacent site, called Bayside, had an earlier, but slower, start and took a more incremental approach than the Quayside plan. In 2010, Waterfront Toronto awarded a 13-acre site to the established U.S. commercial real estate company Hines, who brought on a Canadian partner, Trident, to build the first residential buildings. Hines's own commercial project, T3 Bayside, planned for a pair of office buildings designed by the Danish architect 3XN, through their New York office. The first building began construction in 2020 and was completed in 2023.
The design followed Hines's branded "T3 concept," which promoted the values of Timber, Transit, and Technology. Like the first T3, designed by Michael Green and completed in Minneapolis in 2016, T3 Bayside referenced the architecture of early warehouses - box-like blocks with large open floors - adapted to offices for creative companies. The planned twin building has yet to start construction.
T3 Bayside
Toronto, Canada, 2023
Developer: Hines
Architect: 3XN
Engineers: Magnusson Klemencic Associates, TMP Engineering
Model courtesy of 3XN
Burrard Exchange
Vancouver, BC, Canada
Architects: KPF; Adamson Associates
Engineer: Glotman Simpson Consulting Engineers
Client: Hudson Pacific Properties
All images courtesy of KPF
BURRARD EXCHANGE
Burrard Exchange is a Mass Timber 16-story office building in Vancouver, designed by KPF to integrate into the preservation and renewal of the 1970s Bentall Centre, once the city's premier office complex. The structure is a hybrid concrete and timber composite that uses the strength of precast concrete columns to allow for the height of the building and glue-laminated (Glulam) timber girders and purlins to frame the floors. CLT floor panels with an acoustic concrete topping complete the system. This use of a hybrid construction reduces the embodied carbon by 51%, and weight by 45%, relative to a comparable building of traditional steel and concrete construction.
Building with Mass Timber presents several challenges for tall buildings, including strict building and fire codes. For buildings over 6 stories, column sizes at the base can become too large for a viable office floor plate. The design for Burrard Exchange uses an innovative structure to achieve 30’ column spacing – ideal for office space. The beams are dropped to allow the mechanical ducts and other systems to pass above the timber structure, ensuring that the natural material is the most prominent feature of the interior space. The light weight of Mass Timber was critical to the design, as the building straddles an existing underground transit tunnel.
KPF designed the Burrard Exchange with a simple rectangular massing that steps back at multiple levels, providing many of the office floors with outdoor loggias or terraces. The top floor features a rooftop terrace. Inside, the building’s loft-like structure creates a light-filled biophilic workplace.
Terrace House
Vancouver, BC, Canada
Architect: Shigeru Ban Architects
Engineers: Read Jones Christofferson; Création Holz; Equilibrium
All images courtesy of Shigeru Ban Architects
TERRACE HOUSE
Shigeru Ban is an architect known for his innovative work in timber, paper, and bamboo. His firm, Shigeru Ban Architects (SBA), has a strong commitment to environmental awareness and sustainability. Terrace House is SBA's design for a 19-story (230ft tall), 20-unit hybrid mass timber condominium in Vancouver, British Columbia.
The building’s form is a direct response to three primary site conditions: the neighboring landmarked building, by Canadian architect Arthur Erickson; the desire not to cast a shadow on the nearby park; and preserving existing view corridors toward the waterfront and mountains.
The building has a concrete structure for the podium, tower, and core, and timber structure for the building’s triangular apex.
The timber structure is in counterpoint to the concrete ‘base’ of the building and is intended to create a clear distinction between the base and upper floors. Timber is used because it is a locally available and natural material with demonstrated performance advantages. The Mass Timber has dual function as both structure and an architectural finish.
The timber structure consists of heavy timber posts and beams that have been oversized by 90mm to achieve a 2 hour fire rating. The floor deck is a hybrid timber deck with 5” concrete slab on top. All of the timber structure is fully exposed inside the residential units as the final finish.
The advanced engineering and coordination of the structure –which is supported by a multi-national design team including Canadian, Swiss, Japanese and American designers - will demonstrate the creative potential and efficiency that wood design can achieve in a project of this scale.
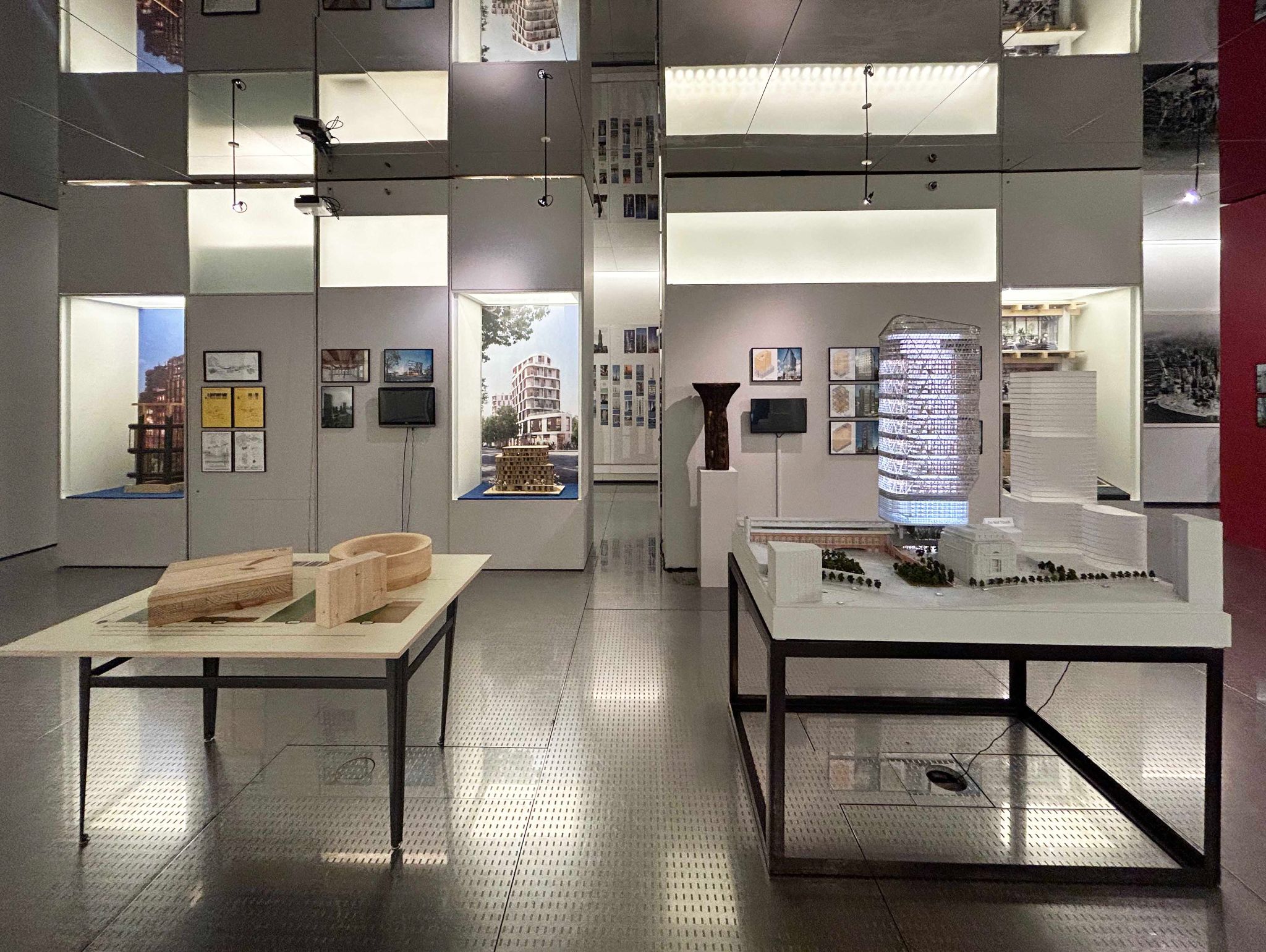
HEIGHT AND HYBRIDS
ATLASSIAN CENTRAL
Australia embraced Mass Timber at about the same time as North America, but their first tall building in the material, 25 King, was completed in 2018 in Brisbane, a city that, like Melbourne, encourages skyscrapers. In more circumspect Sydney, high-rise development has recently boomed and there is a 42-story hybrid steel, concrete, and Mass Timber tower now under construction that will become the world’s tallest (largely) Mass Timber building when it is completed in 2027.
The model in the middle of the gallery of Atlassian Central, the headquarters for a major Australian software company, is a mixed-use office building and urban complex that is part of the redevelopment of a heritage site, Sydney’s main railroad terminal, called Central. The tower is designed by the New York firm SHoP, in collaboration with the local architect BVN. The structure is an ingenious hybrid — a steel diagrid carries the glass facade and open atria around a concrete core with cantilevered platforms every four stories that carry the weight of the load-bearing Mass Timber office floors. The wood creates a biophilic environment for the office workers and the interior gardens and multi-story terraced roof gardens at the top of the tower open to the sky to expand the connection to nature.
Atlassian Headquarters
Sydney, Australia
Architect: SHoP Architects and BVN
Engineers: Eckersley O’Callaghan and Taylor Thompson Whitting
Client: Atlassian and Dexus Property Group
Model and renderings courtesy of SHoP Architects

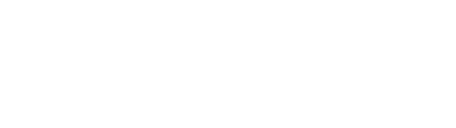
TALL TIMBER is supported, in part, by public funds from the New York City Department of Cultural Affairs in partnership with the City Council.
TALL TIMBER is made possible by the New York State Council on the Arts with the support of Governor Kathy Hochul and the New York State Legislature.